DEP MeshWorks - Welding
Rapid welding process allows you to create welds with specific profiles and
Heat Affected Zones (HAZ) to analyze stress and crack propagation 
Reduce up to 60% of the time to create welds in your simulation model.
User-friendly, requiring minimal input and advanced welding capabilities.

Challenges in welding
Typically, modeling for welds is very time consuming and difficult. This process requires a very experienced engineer with a unique skill set for modeling the welds with specific profiles.
Fast CAE modeling
MeshWorks can address different types of solid welding for fabricated structures that can address various modelling scenarios with very minimal inputs. This process can be executed even by an entry level engineer. One big advantage is the welds can also be used for parametric studies.
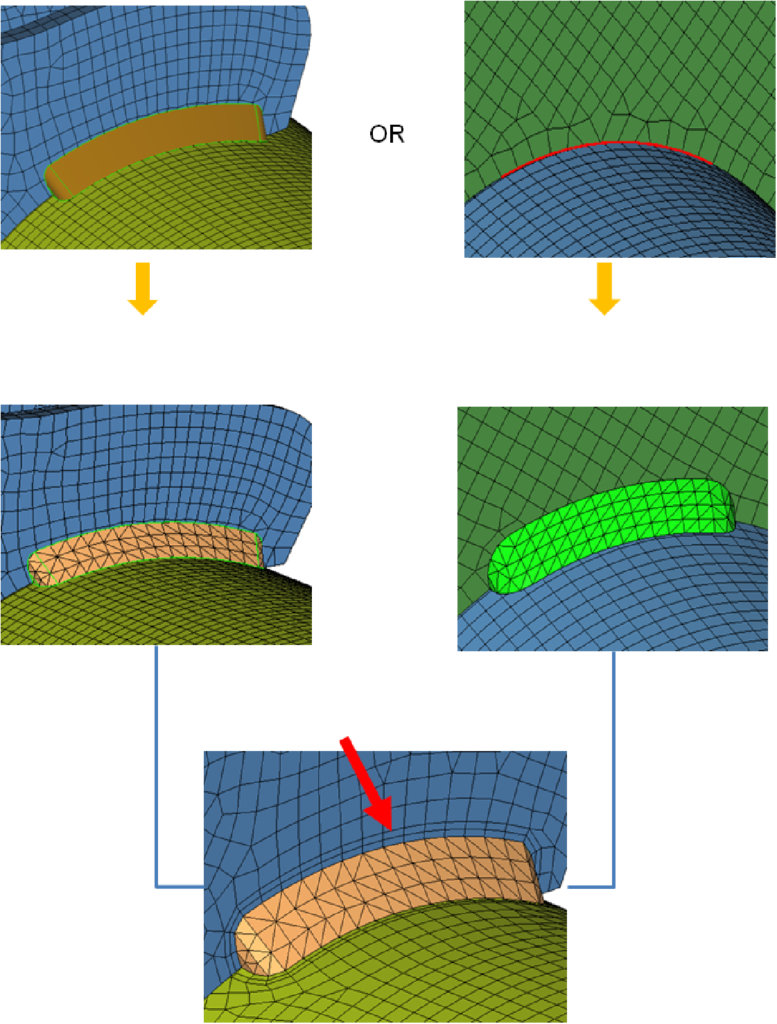
Different profiles and fabrication requirements
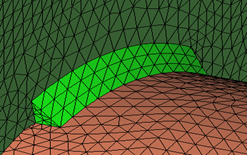
Flat
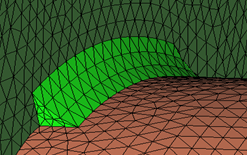
Concave
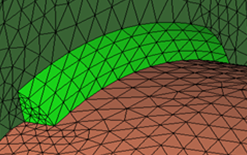
Convex
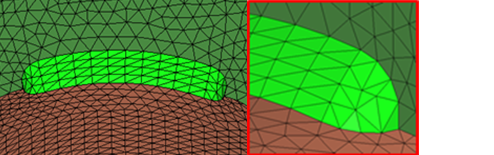
Tapered
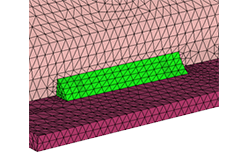
Convex & Concave
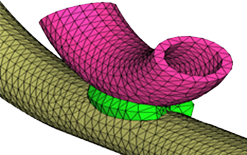
Oval

Circular
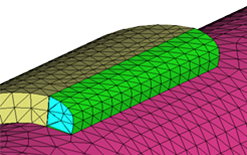
Arc
Why DEP MeshWorks in welding?
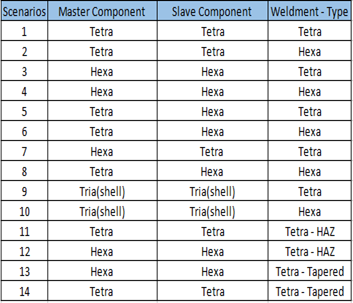
Unique welding capabilities
Tet-Quad-Tetra-Hex mesh combinations including Tapered
HAZ automatic detection
Find all the DEP MeshWorks Solutions
Meshing
Template based meshing allows users to set-up templates for feature recognition, mesh
size requirements and quality criteria.
Modeling
Full simulation set up including materials, loads, BC, automatic 3D welds creation and mid-plane extraction.
CAE Parametrization
Regular FE/CFD models can be converted to intelligent parametric FE/CFD models automatically.
Design Enablers
Create ‘ready-to-use’ enablers as Beads,Darts, Bulk-Heads, Holes/Slots, Part, Shell Rib, Tetra- Rib, Extension/Contraction, Reinforcements, etc.
CAD Morphing
Morph existing CAD data (Body structures, Powertrain and Chassis parts) directly to new
shapes rapidly.
CAE Morphing
Component and full system level FE/CFD models can be morphed to fit target design features.
Welding
Automatically create the weldments and have node-to-node matching connection to the
surrounding parts.
Bolts
Full bolted connections can be easily created. Detail metric bolt, modeling, screws, through bolts.
Concept modeling
Template based meshing allows users to set-up templates for feature recognition, mesh
size requirements and quality criteria.
Parametric Optimization
Parametric models can robustly generate multiple runnable analysis data sets given a Design of Experiments (DOE) matrix.
Topology Optimization
Non-Parametric CAE models enable Multi
Disciplinary Optimization to meet design targets, minimize product weight and minimize manufacturing cost.
And a lot more…
find all the features of
DEP MeshWorks